
WHAT IS THE “BEST” ROOF FOR MIAMI OR SOUTH FLORIDA?
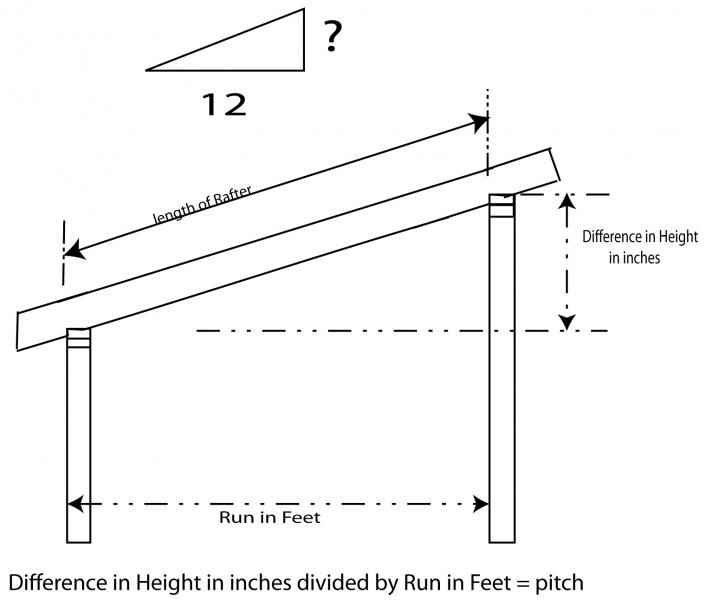
People often ask me what is the best type of roof for Miami or South Florida. Sometimes they ask what kind of roof I have on my own house north of Coral Gables. I always tell them, the best roofs are roofs that last, and in South Florida, roofs that will last depend on the structure of the building they sit on top of. Miami roofing contractors work on a broad variety of South Florida roofs because Miami is a community with a variety of styles of architecture _ each one requires a different kind of roof.
Very few roofing contractors in Miami and South Florida have the experience to deal with all the various conditions local roofs may face. Anthony Wilson Roofing, in business for decades, understands your unique roof needs. And we want you to understand it too. Below is our best explanation of the needs and potential pitfalls for a South Florida homeowner or business owner who needs a new roof.
Best roofs versus roofs that last
I suppose the public perception is that there might be some universally accepted best or premium roof system that is better than all others for our conditions in South Florida. The answer is there really isn’t.
The primary reason for this is that roofs have to be installed on Miami buildings and houses that each present different conditions and challenges for both installation and weathering and serviceability.
The National Roofing Contractors Association as well as the South Florida Building Code and the Florida code create the first and most obvious delineation based on the roof’s slope. (Some refer to this as pitch. It is expressed as “rise over run.” This means that if you measure 12 inches of roof surface from the bottom edge – going up hill – and the elevation increases 2 inches in that 12 inch distance – the slope is expressed as 2 in 12 – usually written 2:12).
Low slope is defined as roofs with less than 2:12 slope – for which our code in South Florida requires a “continuous roofing system.” Continuous simply means this is a fully sealed membrane of some type _ like a fiberglass or modified bitumen hot-mopped system or a rubber or TPO membrane.
For slopes above 2:12 or 3:12, most “discontinuous” roofing systems may be installed in South Florida. These systems are also called “water-shedding” systems because they function as individual pieces that shed the water to each subsequent piece downhill. Most residential sloped roofs use systems that fall within this category. Tile, shingles of all types, metal and slate are all examples of this type of roof.
So, the real answer to the question of what is the “best” roof in South Florida? is it’s the one that is most able to deal with the particular slope, environmental, and traffic issues that it has to deal with within its life cycle.
So what should a South Florida home or business owner look for in a roof?
Roofs that last in South Florida can be hard to come by, but they’re easy to build. It’s all a question of a basic understanding of roof engineering – and not cutting corners.
In general, discontinuous roofs perform better at steeper slopes than their code or practical minimum. We recommend a minimum slope for discontinuous roofs of at least 4:12 – this is a much safer minimum for Miami and South Florida roofs.
Continuous roofing systems perform well from “dead flat” up to and above 2:12 slopes. These systems may also be installed at steeper slopes where the typical limiting factor is whether the system provides the appropriate fire rating.
All roofs in Miami can suffer from vegetative debris that falls on or accumulates on their surfaces, as this impedes water flow and drainage. Asphalt, shingle and metal roofs are also easily damaged by things like sweeping palm fronds here in South Florida, which damage the surface of these roofs. Tile roofs suffer such assaults better.
Many tile roofs are installed here in South Florida as a type of hybrid roof – they utilize a sealed membrane underlayment that is then covered with the discontinuous tile system. This is often the best solution for a homeowner or business owner who wants a roof that will survive South Florida weather. At Anthony Wilson Roofing, we offer roofing systems designed to take advantage of both technologies, with upgrades that can be hard to find in the industry, like synthetic paper barriers that are longer-lasting and more weather impervious than the traditional tar-paper often installed under tile. We also offer upgrades to take advantage of the fact that if you’re installing a new roof to also install extra insulation. We find this option can be a true cost-saver for our clients and helps them mitigate the draftiness of homes that were built before any of us were concerned about energy efficiency. Many of the homes we’ve worked on were originally built without air conditioning and we’ve found this extra layer of insulation in the roof can dramatically lower homeowner cooling costs.
And please be advised – for the most part, the South Florida Building Code is primarily concerned with wind uplift issues. We at Anthony Wilson Roofing are also concerned about wind issues and we work hard to ensure our roofs meet every code for wind, but we advise our customers that there are other issues they should be aware of.
Flashing and other details matter
Many types and methods of flashing that have been considered outmoded and antiquated are still allowed, because the code is still a “minimum” standard. When you compare roofing proposals, each type of flashing, for every junction and penetration should be individually specified, as to both material quality, as well as exactly where in the construction of the roof system (a metal flange for instance) the flashing component will end up.
Roofs that last are hard to define, but easy to identify.
In summation – the real answer is to avoid labeling. Each building in South Florida is different and has different needs for a solid roof. And roofing details, like the flashing and junction construction can be far more important than the use of “best” multi-ply or “best” roof membrane material. At Anthony Wilson Roofing, we take all of these important details into account, working to ensure that our roofs can stand up to South Florida conditions for years to come.
- Anthony